If you’ve decided it’s time to replace the clutch on your manual-transmission car, you’ve reached the point where advantages (crisp, new-feeling response) have come to outweigh disadvantages (significant labor costs or time spent doing it yourself). Whether you don’t have a choice because your old clutch slips badly, or you want to take initiative and upgrade your vehicle by sharpening performance off the line, you have high expectations about the finished result once high labor costs are paid or you’ve spent a lot of time and effort doing it yourself. You’re anticipating silky release and take-in of the clutch pedal, smooth running without harshness or vibrations, crisp shifts that chirp tires on pavement, and the fact that your vehicle feels brand new again. Knowing what’s important when a clutch job is being done can get you those results and save you money, because taking shortcuts usually yields disappointment.
This article focuses on the three integral parts that are part of a manual transmission clutch, what each one does, how the parts relate to one another, and why it’s important to replace all of them together. Most front-wheel-drive vehicles require 8-11 hours of labor to remove a brake assembly, wheel hub, and entire axle on one side in order to separate transmission and engine for clutch access. Many rear-wheel-drive cars require only 4-5 hours of labor because all that’s needed to slide the transmission out of the way is dropping the driveshaft. Whatever the installation process is for your vehicle, you’ll find the cost of replacing all these parts still isn’t that high compared to shop labor or the value of your time.
It’s also important to remember that a clutch is an integrated system where all the parts depend on each other. Replacing them as a set is the smartest thing to do. If the vehicle has a pilot bearing which supports the end of the transmission/transaxle input shaft, replace that as well. Worn pilot bearings will cause misalignment of the shafts, leading to fast wear of clutch and throwout bearings as well as problems during engagement and disengagement.
WHAT A “CLUTCH” ACTUALLY CONSISTS OF
A manual transmission “clutch” is actually made up of three main parts positioned between the engine’s flywheel and the transmission input shaft. As clutch parts engage, they allow smooth coupling and uncoupling of the drivetrain through slippage as the clutch disc pad and flywheel come together to transfer driving force to the wheels. They can be clamped firmly together, disconnected entirely, or allow for an infinite amount of “slip” against the flywheel’s face so that a vehicle can begin moving forward or backward progressively.
A clutch disc is a rotating circular metal plate splined to the transmission input shaft that’s covered with friction material on both sides. The disc is located closest to the engine flywheel in front of the clutch pressure plate, and is clamped tightly between these two members when the clutch is engaged. Clutch discs may also be described as friction discs.
The clutch pressure plate (simply known as “pressure plate”) is a spring-loaded metal plate that spins with the flywheel and applies pressure so that the clutch disc becomes firmly clamped against the flywheel. When the clutch is engaged, springs between the pressure plate and a separate cover piece force the clutch disc against the flywheel.
A throwout bearing (or “release bearing”) is the component that pulls the pressure plate and clutch disc away from the flywheel to disconnect the engine from the drivetrain, then pushes everything back together when the clutch is engaged again. The throwout bearing does wear and, in extreme cases, will squeal when the clutch pedal is depressed.
WHAT IT MEANS WHEN CLUTCH COMPONENTS WEAR

This picture shows an example of a clutch disc that’s worn to the point where hardly any friction material is left on the surface.
By nature of what clutch discs are designed for, their surface coating of friction material is under a constant state of wear whenever slippage occurs during the normal process of letting the clutch in. Naturally, a clutch disc needs to be replaced as a wear item. However, it’s also important to note that virtually any problem with other clutch components usually leads to uneven wear on the clutch disc, causing a scenario where the flywheel surface can become scored or even warped if heat conditions become excessive. So even if another clutch component is found to be the source of a problem, replacing the friction disc will keep you out of trouble.
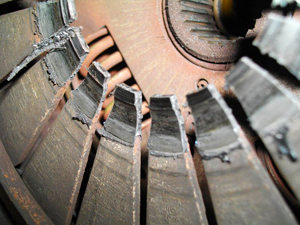
The spring fingers on this clutch pressure plate became damaged due to misalignment caused by a collapsed throwout bearing.
Like any spring-loaded device, a pressure plate’s springs (or “fingers”) tend to weaken over time and cause clutch slippage from lack of pressure. This problem is almost impossible to tell by looking at a pressure plate that been subject to normal wear, but one that is severely worn will usually make a rumbling or growling sound when the clutch is engaged. As throwout bearings wear, they can cause misalignment issues that cause damage to other components.
CLUTCH KIT PACKAGES
Clutch discs, pressure plates, and throwout bearings are often sold in sets together and priced lower than the cost of buying replacement components separately. Depending on vehicle design and manufacturer recommendations, some kits may also include pilot bearings for the input shaft. In many cases, manufacturers will only offer these items together as a complete kit because they feel if a clutch disc has reached the point of wearing out, related components have reached that point as well. If the engineers that designed, built, and tested your vehicle observed these conditions in order to reach that conclusion, their advice is well worth heeding.
FLYWHEELS – WHEN THEY SHOULD BE CHANGED
Since your old clutch disc has had a direct relationship with the engine’s flywheel over many miles, inspecting the flywheel when things are apart is essential. The most important thing to check is the flatness of the flywheel because any small degree of warpage (or “runout”) will cause problems. Using a dial indicator or a straight edge across the flywheel at different points will give an indication if there’s any wobble. Some manufacturers say runout up to .005 inch for every inch of flywheel diameter is acceptable, but many automotive engineers feel anything over .002 inches of runout per inch will create noticeable vibration, clutch chatter, and related issues. It’s a safe bet that anything over .005 inches creates the risk of clutch failure from extreme vibrations.
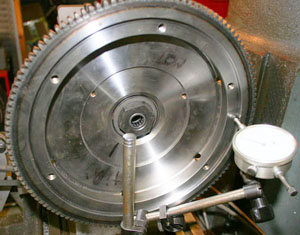
It’s important to check the flatness of your flywheel with a dial indicator (shown here) or a flat edge. Any runout should be addressed.
Inspect the flywheel for cracks – especially around holes for mounting bolts. If cracks are deeper than surface scratches, the flywheel should be replaced in order to avoid the likely possibility it will shatter at high rpms and damage the transmission itself. Dual-mass flywheels consisting of two sections bolted together should never be resurfaced because of balance issues likely to be created. Check the starter motor teeth around the circumference of your old flywheel to make sure none have broken off.
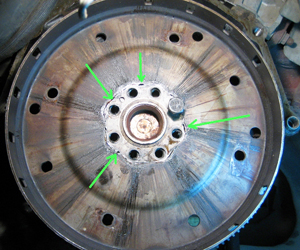
Cracks anywhere on the flywheel surface pose a risk of the entire flywheel coming apart and damaging transmission internals. Replace it with a new one.
Reviews are mixed and opinions vary on the subject of resurfacing flywheels when doing a clutch job. Some vehicle manufacturers strongly advise against any resurfacing and recommend flywheel placement if the old one looks questionable. The internet is full of horror stories from users who have had to take their transmission back out and replace the flywheel after bad vibrations occurred. Yet others swear by the process, saying clutch discs grab better because of the fine, even ridges left after a lathe grinds surface metal flat again. One vehicle owner who didn’t resurface his flywheel when installing a competition-grade clutch claimed he did not see performance benefits until he took the trans back out to do so.
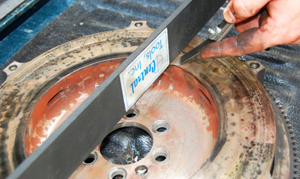
Using a straight edge and feeler gauge is another effective way to determine if there is runout on flywheel surfaces.
Because flywheels often get scored and hotspotted with hardened patches during thousands of miles of performance driving, leaving an old flywheel as is will definitely shorten the lifespan and function of any new clutch being installed. If your clutch disc became extremely worn and failed, odds are very high your flywheel is scored enough to require replacement. Unless you enjoy dropping the transmission out of your car on a regular basis, we recommend replacing any flywheel that isn’t perfect when doing a clutch the first time. Simply put, a new flywheel will work properly every time you install it, but resurfacing is prone to problems.